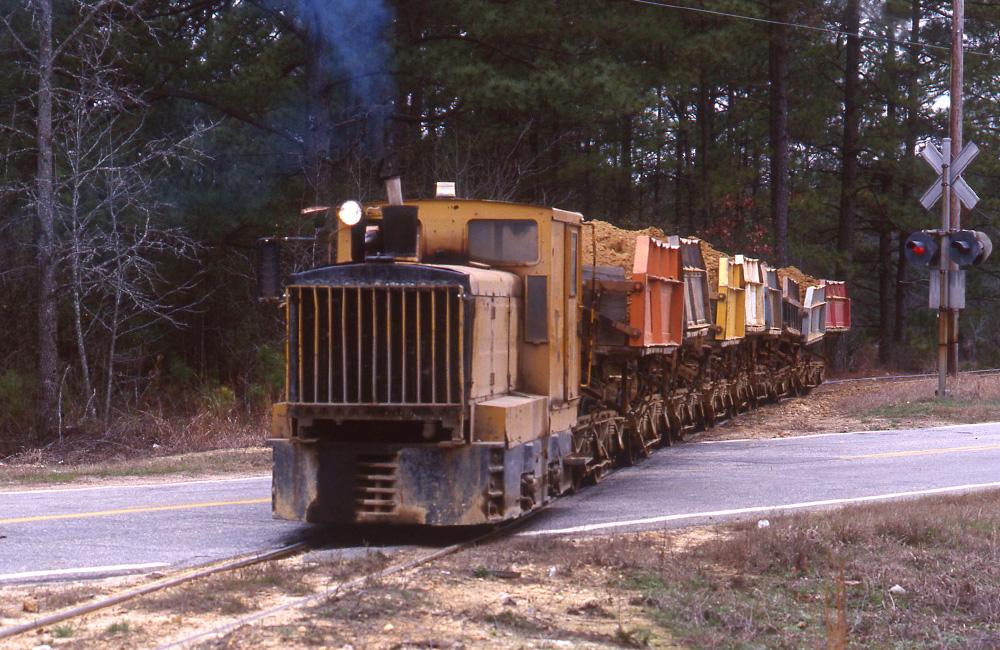
With larger railroads, you seldom see the big picture. You see trains passing a given location, but unless you have access to loading manifests, you seldom know the origin and destination of any single car or even what it is carrying.
That can never be said about the Palmetto Brick Company Railroad, however. Its entire length is only about 2 miles, almost all of which is visible from a public highway. It doesn’t interchange with any other railroad, because it’s a landlocked 3-foot-gauge operation. Yet, at the same time, it’s a railroad any efficiency expert would love.
Located just south of the North Carolina-South Carolina border east of Cheraw, S.C., the Palmetto Brick Co. mines clay within a few miles of its sprawling plant near the Pee Dee River. We may not think of the digging of clay as a mining operation, but technically, it is. That clay is hauled to the plant in small unit trains by tiny narrow gauge diesel locomotives.
The operation, which has remained essentially unchanged for decades, makes it a perfect railroad you can model, either as a stand-alone diorama or as an attention-getter in a corner of a larger layout.
A unique prototype
Though it’s operationally simple, modeling the Palmetto Brick 3-foot gauge trains could take considerable effort and skills, depending on the level of detail you want and how closely you want to follow the prototype. There are no commercial models of the rail equipment used by the brick plant, though commercial models could be adapted if you only want a generic operation of this type and not an exact depiction.
The railroad you can model is in many ways an anachronism in an age when narrow gauge industrial in-plant railroads have all but disappeared. It even uses some ancient technology, such as link-and-pin couplers. But the operation is still so simple and efficient that no replacement is contemplated.
Almost everything on the prototype railroad has been customized in one way or another. The engines have been rebuilt with diesel motors from front-end loaders. (They originally had gasoline-powered prime movers.) The dump cars have been equipped with wheels intended for intermodal flatcars.
Even track sections have been assembled locally with homemade concrete ties. Yes, the Palmetto Brick Co. Railroad had concrete ties back in 1980, long before they became common on large U.S. railroads.
The brick company railroad operation also used other innovative approaches, such as one-man operation, push-pull trains, and fastening rails to cast concrete slabs at some locations.

Operations
The basic operation of this line consists of one engine working with two sets of dump cars. The process begins with the engine backing an empty train out to the loading location. There, in the middle of an otherwise open field, an excavator (previously a dragline) loads the cars. The train operator repositions the train as necessary until all cars are loaded.
Once the strange-looking top-heavy dump cars are loaded, the train slowly makes its way toward the brick plant, rolling across the line’s singe grade crossing of the road leading to the plant. The grade crossing has working crossing lights, triggered manually by a trip rod on the engines which activates the lights on one side of the crossing and then off again at another switch at the other side of the crossing — a solution some model railroaders have been known to employ!
Just short of the unloading shed, the train comes to a stop. The engine cuts off and pulls past a switch, then reverses to couple onto an empty set of cars. A cable from a winch inside the unloading shed is hooked to the lead loaded car, and the loaded train is winched up an incline into the shed.
There, one car at a time, safety chains that prevent the cars from dumping their loads are unhooked. A hydraulic device tips each car’s dump platform, emptying the clay into a receiving pit. Once the train has been unloaded, it is allowed to roll back down the incline and the cable is detached.
While the first set of cars are unloaded, the engine is already shoving the second set of cars — empty — back out to the clay loading point. Then the cycle repeats itself.
Though Palmetto Brick ships its bricks all over the U.S. by rail as well as trucking completed products to customers in the Carolinas, the plant does not have its own siding. Instead, the company trucks bricks to be shipped by rail to a CSX team track a few miles away. The team track on is CSX’s line south of Hamlet, N.C. But my track plan also includes a standard gauge siding, not present at the Palmetto Brick plant, to better incorporate the plan into a larger layout.
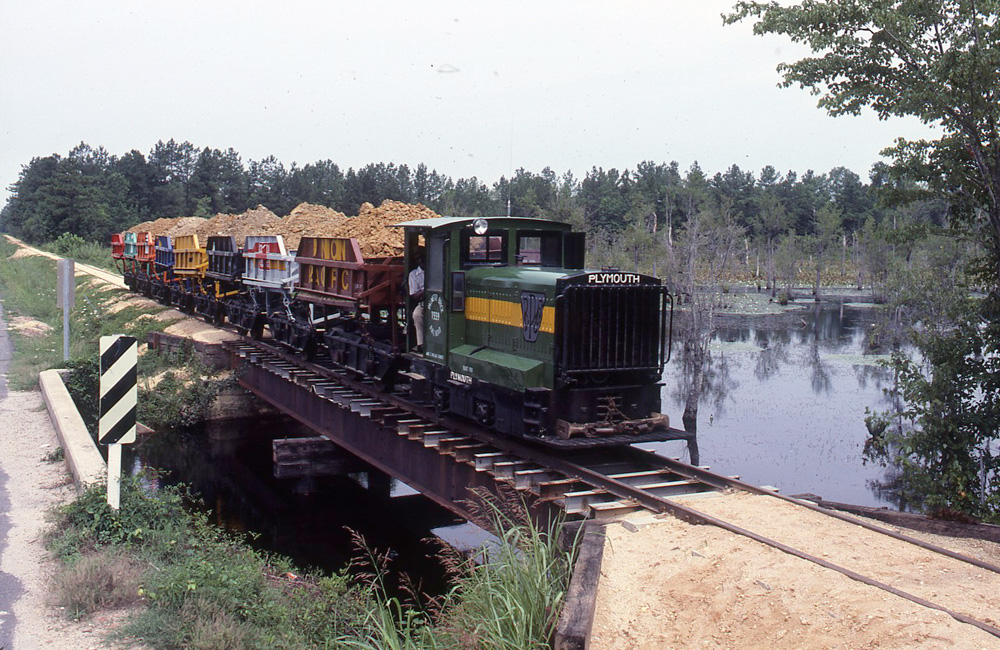
Equipment
The Palmetto Brick Co. operated its railroad with modified 1940-era equipment. The two engines are 10-ton Plymouth DL models that have been remotored (and otherwise extensively rebuilt) by Palmetto Brick.
- 1939, built in 1939 for E.I. DuPont in Barksdale, Wis., was bought by Palmetto Brick in 1955.
- 1946, built 1948 for Richtex Brick Co. of Farmington, N.Y., was later transferred to the Richtex operation in South Carolina. It was purchased by Palmetto Brick when Richtex discontinued rail operations.
The Palmetto Brick railroad began as a steam-powered standard gauge operation. In the 1940s, the line was converted to narrow gauge, apparently because the rails were easier to move as needed.
The cars have no brakes. Only engine braking is used on the very flat line. A safety cable runs the length of each semi-permanently coupled consist.
The brick plant’s own mechanics do all maintenance on the equipment. There’s no railroad shop as such. The plant owns enough cranes and heavy-duty forklifts so that if work needs to be done on an engine or car, it is simply picked up off the rails and moved to a location where the work can be done.
Changes
One of the few major changes in the line in the past two decades has been the abandonment of a spring-switch-equipped passing siding near the highway crossing. That siding permitted simultaneous operation of two trains and three sets of cars during the line’s heyday in the 1980s.
During this operation, car sets were exchanged each time an engine reached the unloading shed. After uncoupling from the loaded cars, the engine would immediately couple onto waiting empty cars and push these to the passing siding, where the train would meet the next inbound train.
The siding was abandoned because of problems with the spring switches (which froze in cold weather) that caused at least one derailment. Besides, with current loading and unloading technology, one engine working with two sets of cars could deliver clay about as fast as the unloading shed could process it.
The loading area in the middle of an open field has been relocated a few times as clay deposits were mined out but has remained basically the same for the last two decades.
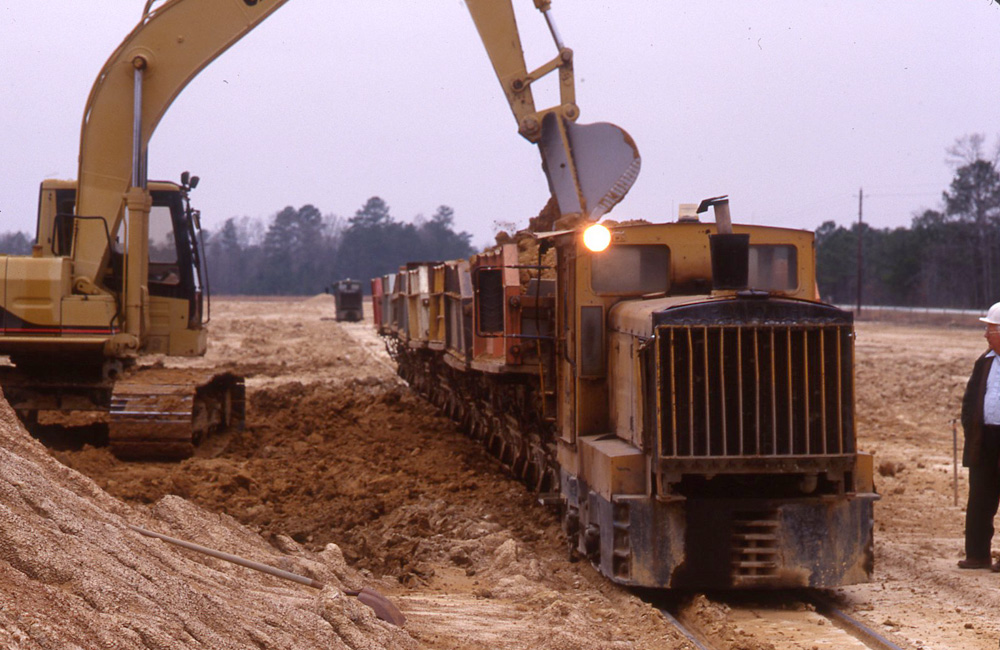
Modeling possibilities
The closest commercially available equipment to that used by the brick plant comes in 2.5 foot (HOe) gauge from Roco of Austria, available in the U.S. from the Walthers catalog and various Walthers retailers. Roco provides a small (albeit six-axle) narrow gauge (HOe) industrial switcher and a set of dump cars, as well as narrow gauge industrial track, including switches.
Though HOe is the same physical gauge as N scale, the tie spacing on N gauge track would be completely wrong for narrow gauge industrial track. N scale mechanisms could, however, be used in scratchbuilding an engine and cars.
Vehicles and other industrial equipment used at the plant and loading site are readily available. Both excavators and draglines are available from several suppliers. Add to these a variety of large and small trucks appropriate to the era. At the plant, you’ll want forklifts and similar equipment.
Structures at any brick plant tend to consist of — what else — nondescript low brick buildings and sheds of various types. These can be provided with either commercially available brick structures or you can scratchbuild your own using plastic brick sheets.
Operationally, you could model the as a true point-to-point. (Yes, this is an operation that you could almost model true to scale!) Or, for an automated feature on a larger layout, you could build a closed loop with a hidden siding that would let you simulate loads-in, empties-out with two identical train sets.
The track plan provided is based on the latter type of operation. The plan features a few attributes of the brick operation but gives up others that would exceedingly be difficult to model, such as the winching of cars into the unloading shed.
Instead, a loaded train proceeds into the unloading shed (remember to model vents on the roof for exhaust fumes) and enters a siding hidden within the plant complex.
Then, after a short delay simulating the unloading of the cars, an identical empty train — with the engine pushing now — heads out to the loading area, moving clockwise around the loop to where it disappears behind a hill/clay pile, but continuing on back into the plant.
Again, after a short delay now simulating the loading of the train by the dragline or excavator, the loaded train emerges from the hidden back side of the plant, proceeding counterclockwise around the loop to the front and into the unloading shed (and then the hidden siding).
Additional equipment can be parked on a short siding near the unloading shed. Many opportunities exist for adding as much detail as you want to the structures and terrain.
The track plan can be built with the Roco HOe 10” radius sectional track. However, the Roco flexible industrial track or even hand-laid track would better simulate the simple nature of the right of way.
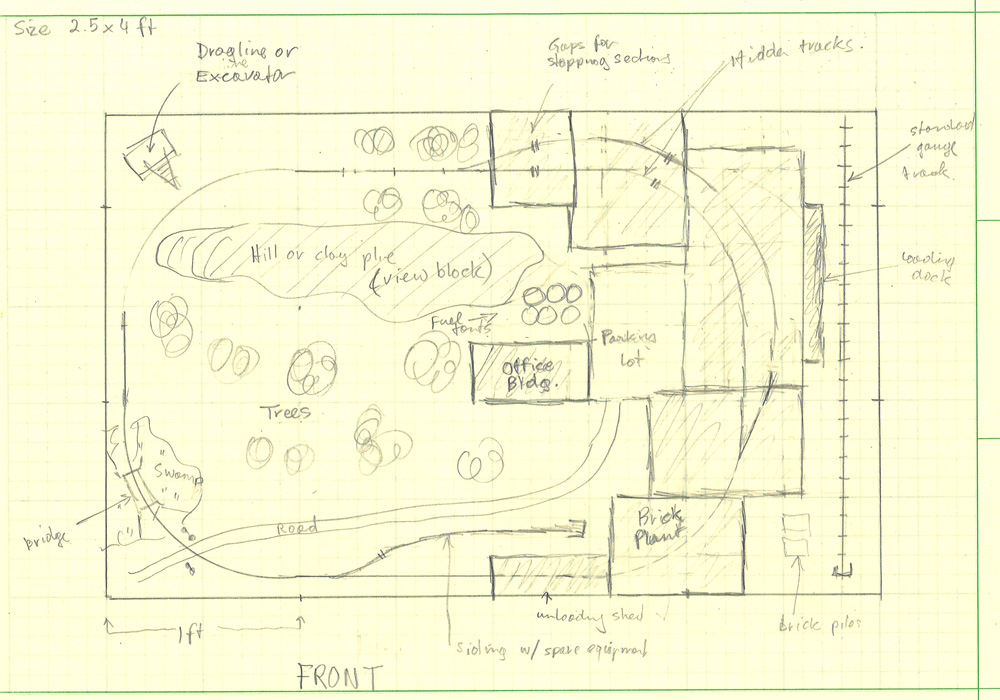
Excellent story! and a good looking model plan.